Servo Presses, AIDA DSF Series Industry Leading Stamping Technology, From 80 - 3,500 Tons
Servo Presses
Single Point Gap & C Frame Servo Presses
DSF-C1-A Models80 - 250 Tons
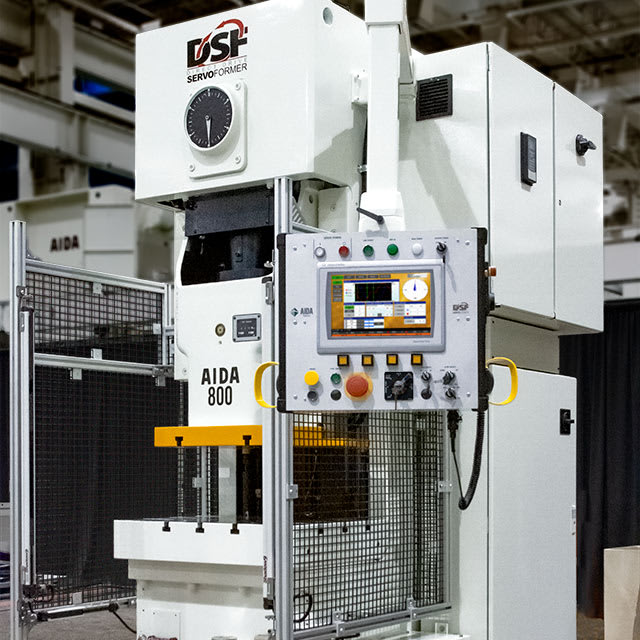
Two-Point Unitized Frame Servo Presses
DSF-N2-AB Models200 - 300 Tons
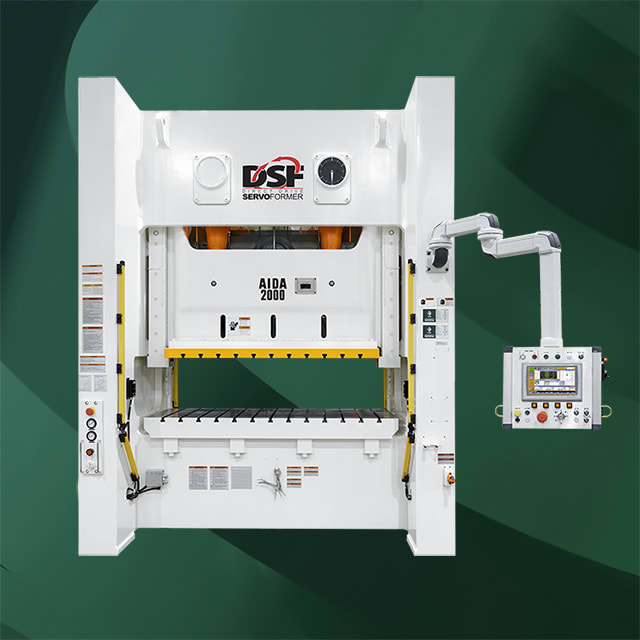
Mid-Size to Large Tie Rod Frame Servo Presses
DSF-M2 Models315 - 1,250 Tons
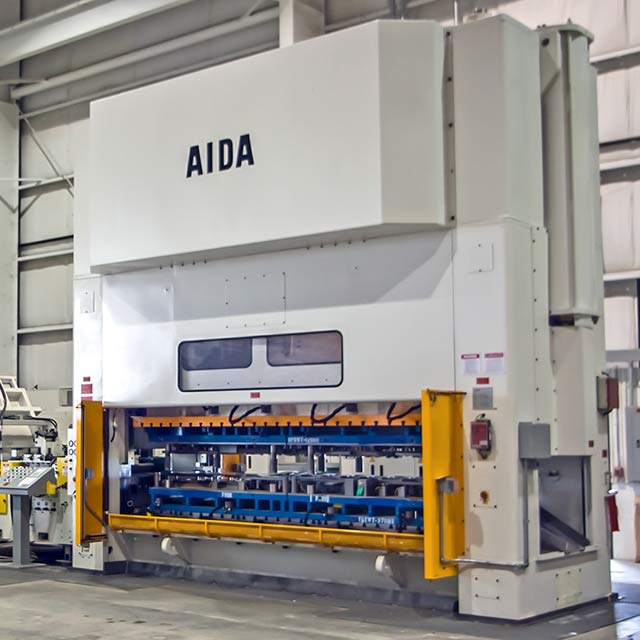
Large Servo Tandem & Transfer Presses
DSF-S2 & DSF-S4 Models800 - 3,000 Tons
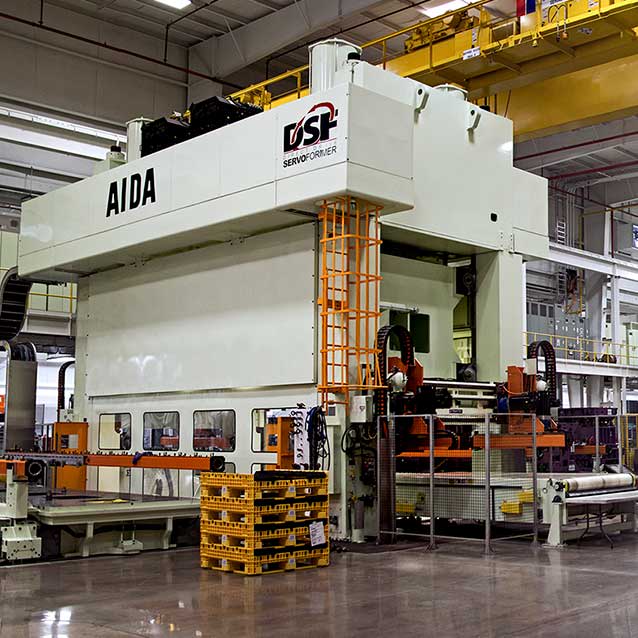
Servo Press Tandem Lines
AIDA's World Class, High Speed Servo Tandem Lines
Servo Press Overview
DSF Series Servo Press Overview
Advanced Servo Press Technology from the Industry Leader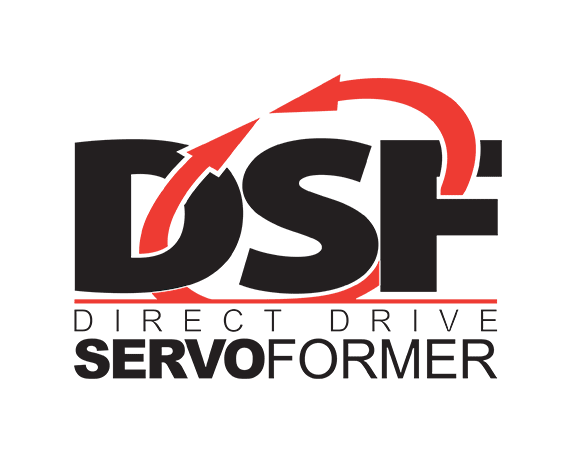
AIDA introduced the world's first direct drive servo stamping presses in 2002. Since that time, AIDA has continued to maintain the position of technology leader in developing servoforming presses. The AIDA DSF Series (Direct Drive Servo Former) servo presses represent the pinnacle of advanced engineering and manufacturing in the metalforming and stamping press industries.
Throughout the world AIDA servo presses produce countless parts across many sectors and industries. From the demanding applications of high strength and ultra high strength steels and aluminums in the automotive industry, to the incredibly precise tolerances needed for the aerospace and medical industries, and for parts of all shapes, sizes and production volumes in between, AIDA servo presses enable manufacturers to produce high quality parts consistently and efficiently.
Technology Features
AIDA Servo Motor
High Torque, Low RPM, Designed and Built by AIDA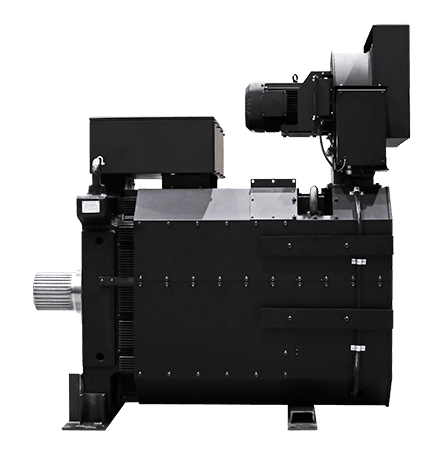
AIDA servo presses cover the widest range of capacities and capabilities available from any press manufacturer, from 80 through 3,500 metric tons. AIDA DSF Series Servo Presses are the most advanced servo stamping presses available. AIDA was the first, and is the industry leader, in direct drive servo presses. At the heart of all AIDA DSF Series servo presses are the AIDA designed and manufactured, high torque, low RPM servo motors.
More About AIDA Servo MotorsProgrammable Slide Motions
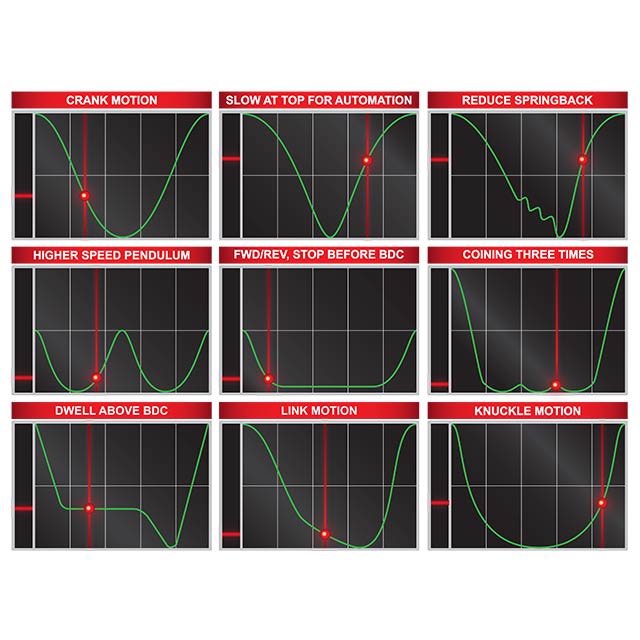
Optimized servo press slide motion profiles maximize metal stamping productivity and improve part quality.
E.C.O. System
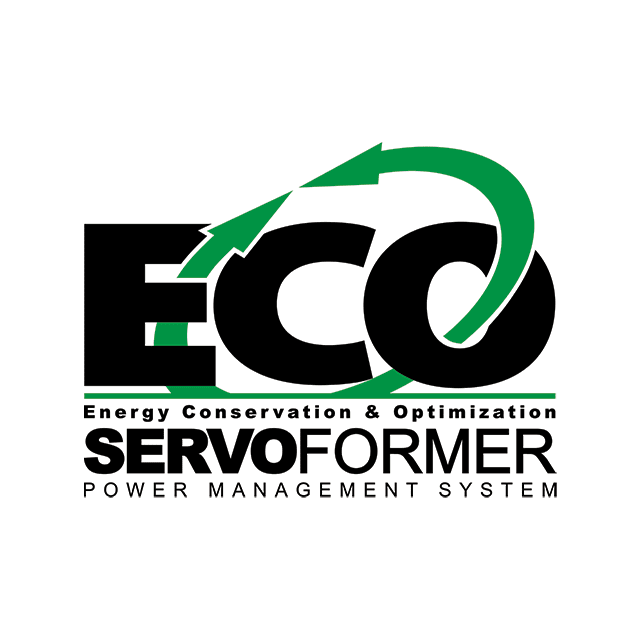
The most efficient servo press energy management system available. The AIDA system stores energy in long life capacitor system (rated over 20 years) to optimize energy consumption.
More About E.C.O. SystemAIDA / Allen-Bradley Servo Press Control
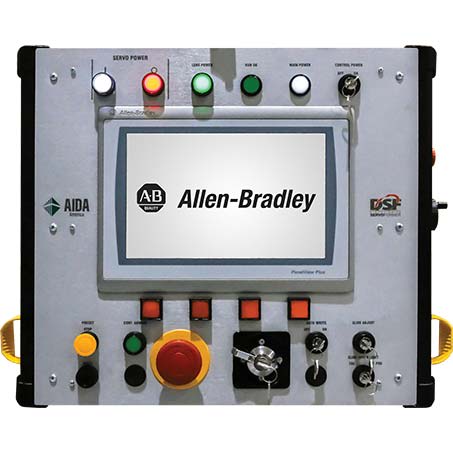
For presses 80 - 300 tons. User friendly design, large touch screen enhances ease of operation. Locally designed and manufactuered to meet North American customer needs.
More About AIDA / Allen-Bradley Servo Press ControlsAllen-Bradley PLC
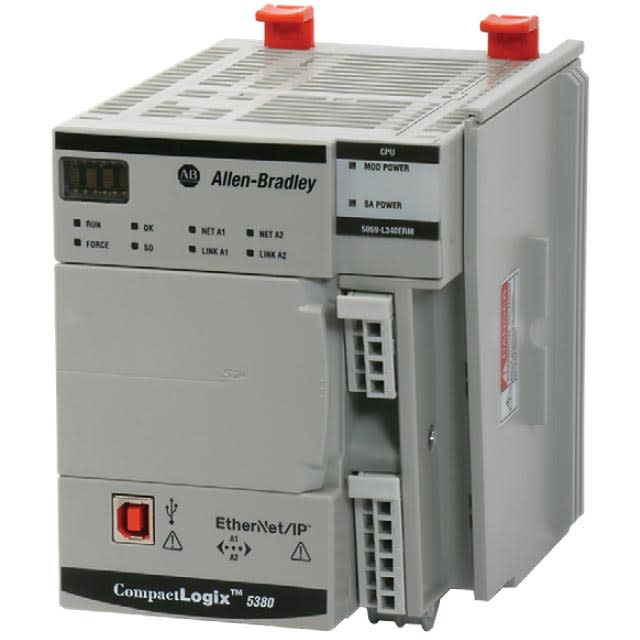
CompactLogix PLC with Beckhoff motion controller for precise control. Locally designed and manufactured to meet North American customer needs.
More About Allen-Bradley PLC Servo Press ControlsCNC Handwheel Control
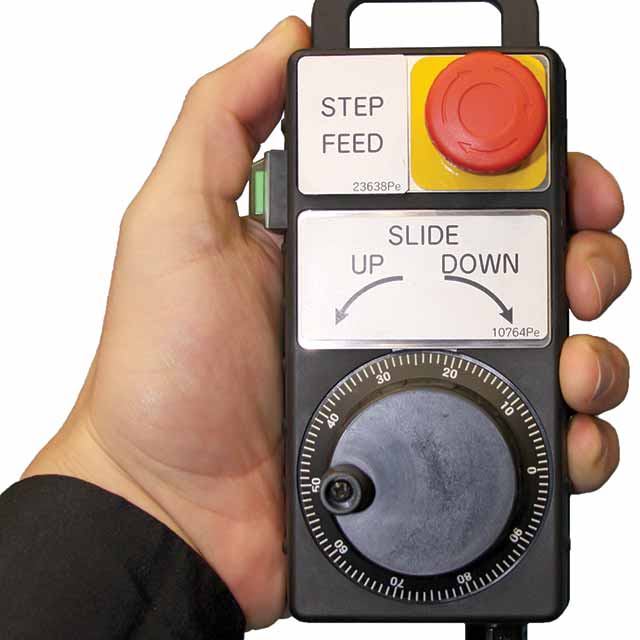
Precise control of your servo press at your fingertips. The answer to die set-up and try-out operations. Step Feed Mode, controlled by the handwheel, allows press operators to cycle the press at below 1 spm.
More About CNC Handwheel ControlMitsubishi Controls
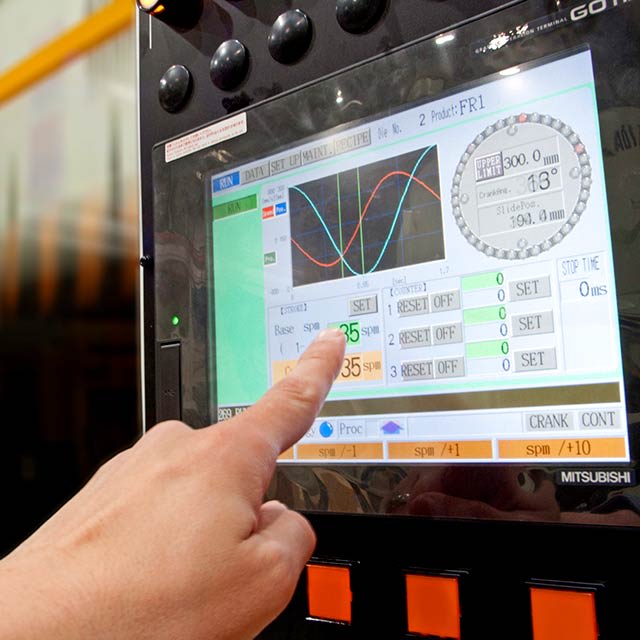
Provides full functionality at an affordable price. Mitsubishi PLC with AIDA motion controller for precise control of your servo press.
More about Mitsubishi ControlsTechnical Resources
Videos, Articles & Additional Information
DSF-M2-6300, 630 Ton Servo PressAIDA DSF Series DSF-M2-6300, 630 ton servo press. This video shows a few examples of the motion profiles available to stampers when using an AIDA servo press. The first direct drive metal stamping servo press was engineered and manufactured by AIDA over 20 years ago and AIDA continues to be a leader in servo press technology. This 630 ton straightside servo press, designed and built at AIDA-America in Dayton, Ohio, shows just a few examples of the flexibility and precision this type of system can bring to a stamping operation. Solve your production volume and part quality challenges with an AIDA DSF, direct drive servo press.
View More AIDA Videos on YouTubeFrequently Asked Questions
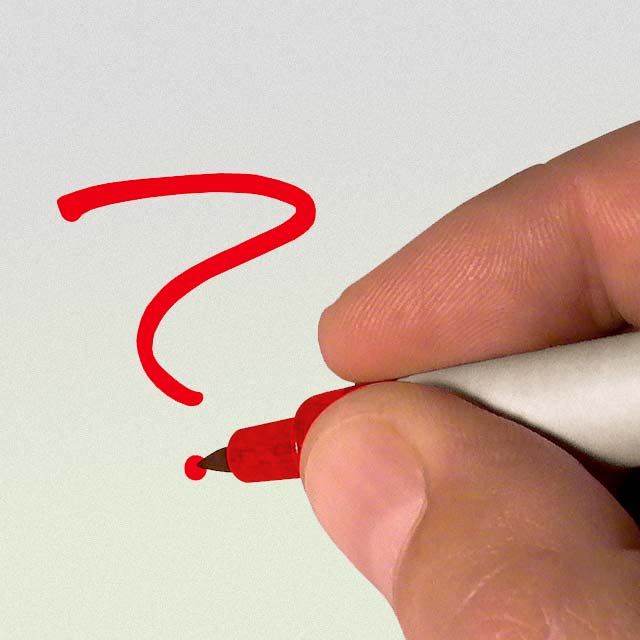
We offer answers for all types of common questions - whether technical in nature or as simple as where to look for career opportunities. Examples of some questions are: What is HOLP? Where is the closest AIDA facility located? How can we get a copy of the manual for our AIDA press? What is reverse tonnage? Visit our frequently answered questions section to find answers to your questions.
View Frequently Asked QuestionsAIDA-Tech White Papers
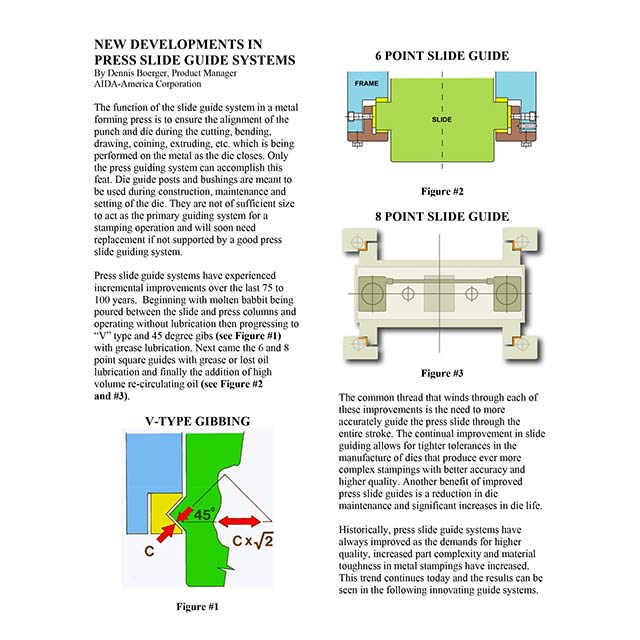
Topics such as connections spacing, slide guiding systems, reverse tonnage and more, AIDA-Tech White papers offer information for a variety of technical subjects related to stamping presses and press operations.
View AIDA-Tech White PapersMetalforming Articles
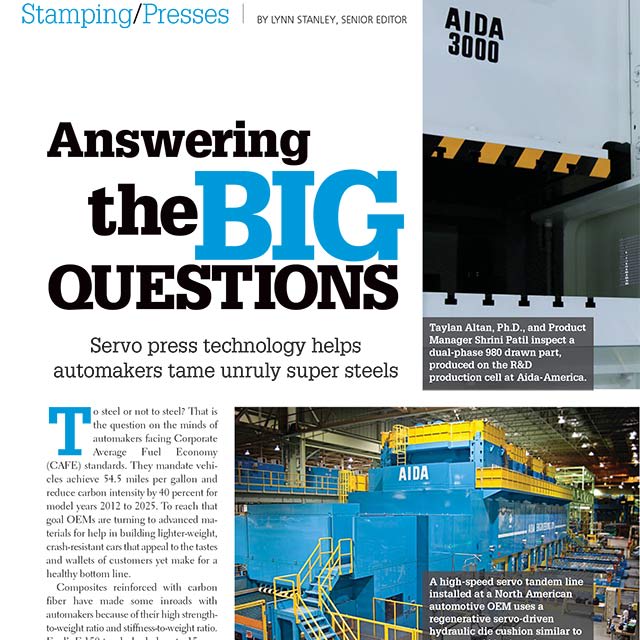
We maintain a library of metalforming articles from a variety of industry publications covering a wide range of topics centered on stamping and press operations. Topics include press technology, market trends, and press applications. Many of the articles collected here have been authored by or contributed to by AIDA associates.
View Metalforming ArticlesEducational Partners & Resources
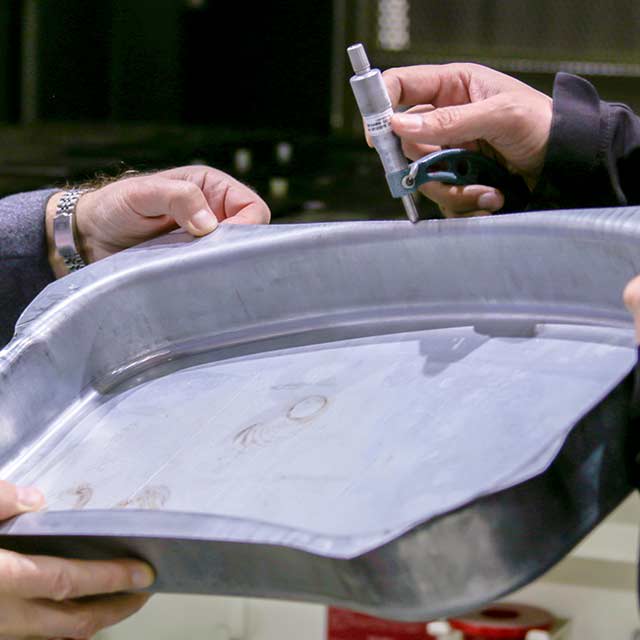
Not only does AIDA invest 5% of annual revenue towards internal research and development, but AIDA also actively seeks and participates in research with educational institutions such as the Center for Precision Forming (OSU), Institut für Umformtechnik, Edison Welding and others.
More About Educational PartnersApplications Studies & Die Trials
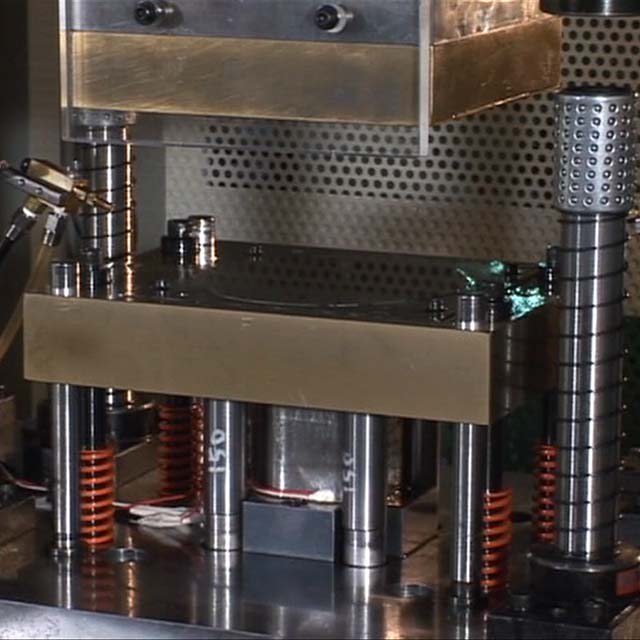
Application studies and die trials provided by AIDA prove, with your own dies and part drawings, how AIDA stamping press technology can have multiple benefits to your manufacturing operations, including increased production rates, higher quality parts, reduced scrap, and reduced maintenance.
Applications Studies & Die TrialsServoFormer Application Training
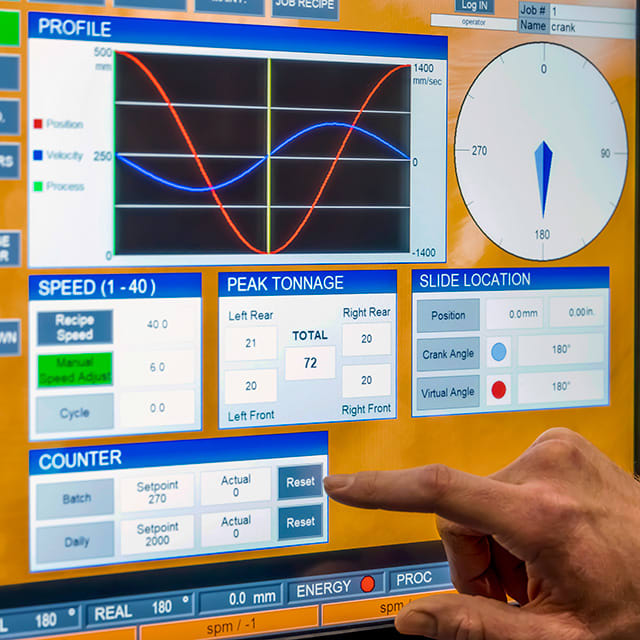
AIDA is a partner for success in understanding and applying servo press flexibility to your opperations. Our experienced Application Engineers will assist in working with your team to ensure top performance is achieved from your servo presses.
ServoFormer Application TrainingServo Press Optimization
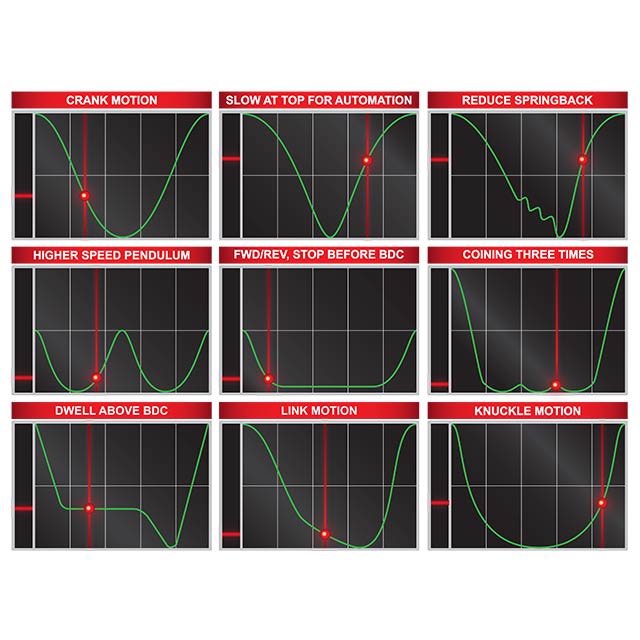
AIDA understands that in order to maximize the benefits that servo press technology can bring the operations must be optimized. AIDA provides on-the-floor stroke profile optimization for maximum productivity.
Servo Press OptimizationStamping Press Technology
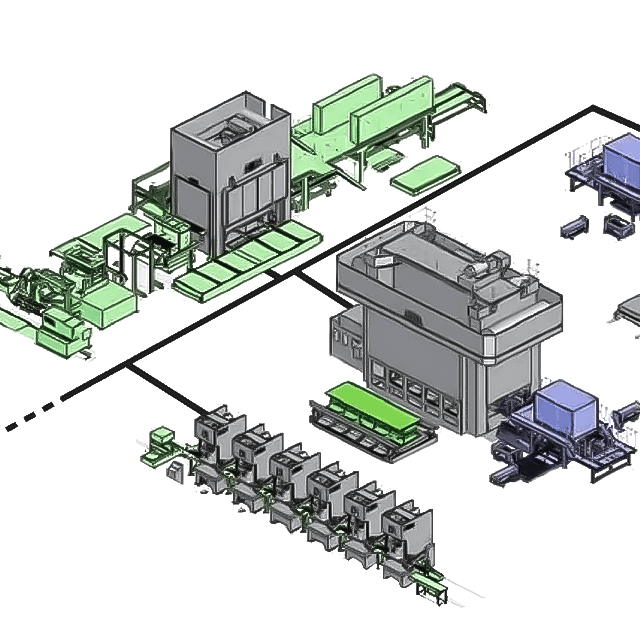
For over 100 years AIDA has been developing and manufacturing specialized metalforming products like metal stamping presses and related automation equipment, such as transfers, robots, and feeders. AIDA's exclusive stamping press technology is used throughout our wide range of presses, from 30 through 4,000 tons capacity.
Stamping Press TechnologyServo Press Technology
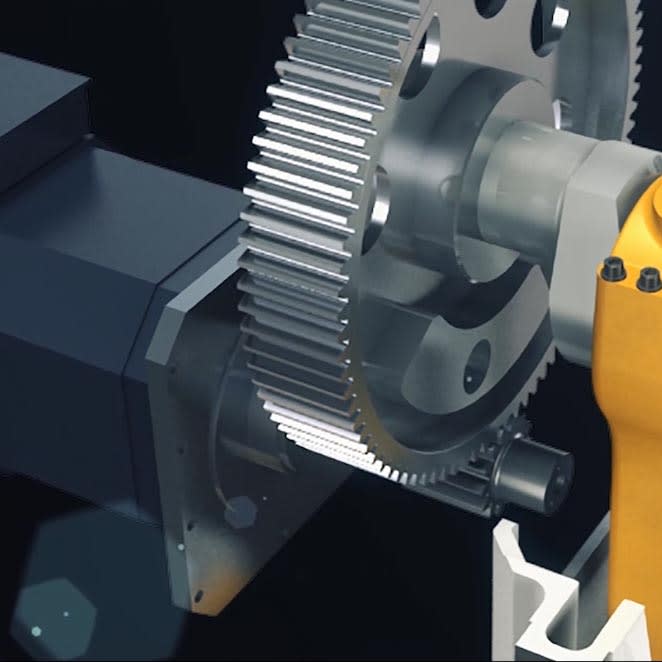
AIDA introduced the world's first direct drive servo stamping presses two decades ago. Since that time, AIDA has continued to maintain the position of technology leader in developing servoforming presses. AIDA DSF Series (Direct Drive Servo Former) servo presses represent the pinnacle of advanced engineering and manufacturing in the metalforming and stamping press industries.
Servo Press TechnologyTerms & Glossary
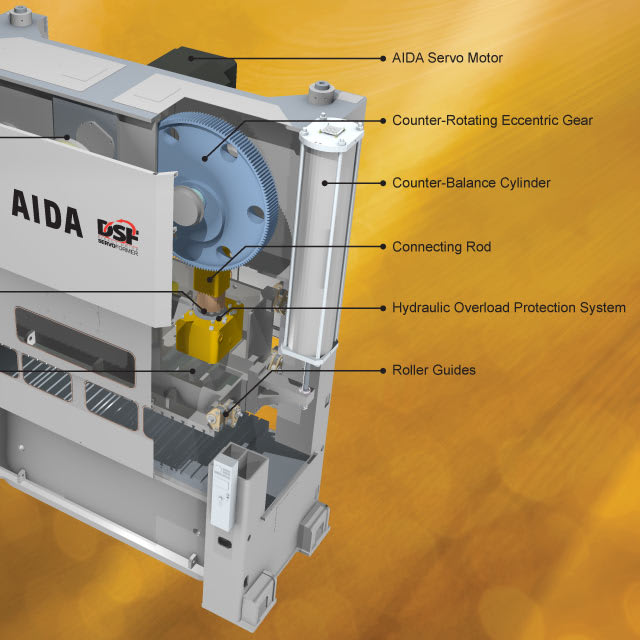
A variety of functions may be performed by many different types of presses, depending upon the tooling. Typical press operations and other terms referring to press features and functions, as well as basic press characteristics and designs are explained in this section of our website.
View Terms & GlossaryUser Testimonials
Ajax Metal Forming Solutions
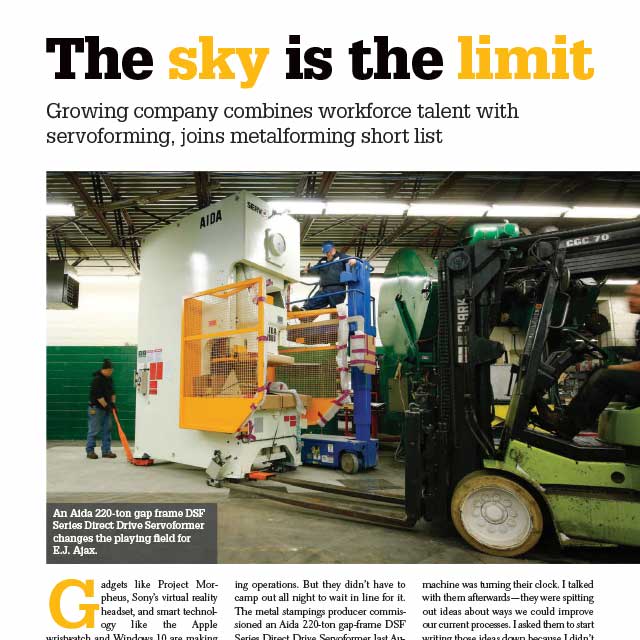
"We needed more capacity and our research told us that servoforming is the direction stamping is taking so we wanted to get ahead of the curve."
View User TestimonialBatesville Tool & Die
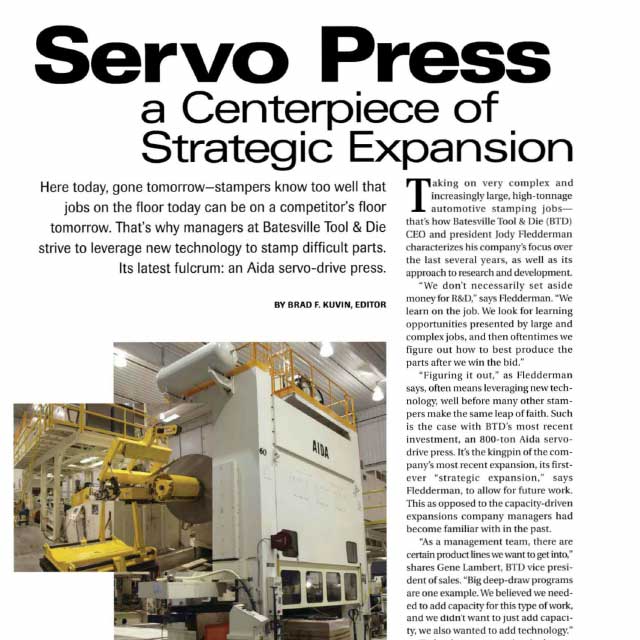
"We believed we needed to add capacity for this type of work, and we didn't want to just add capacity, we also wanted to add technology."
View User TestimonialClips & Clamps
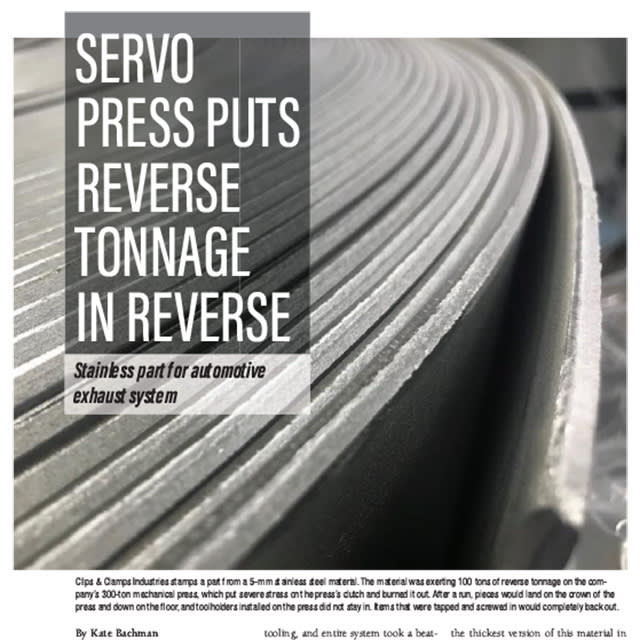
"The fact that servo maintains its tonnage through the stroke at snap-through is just incredible."
Dundee Manufacturing
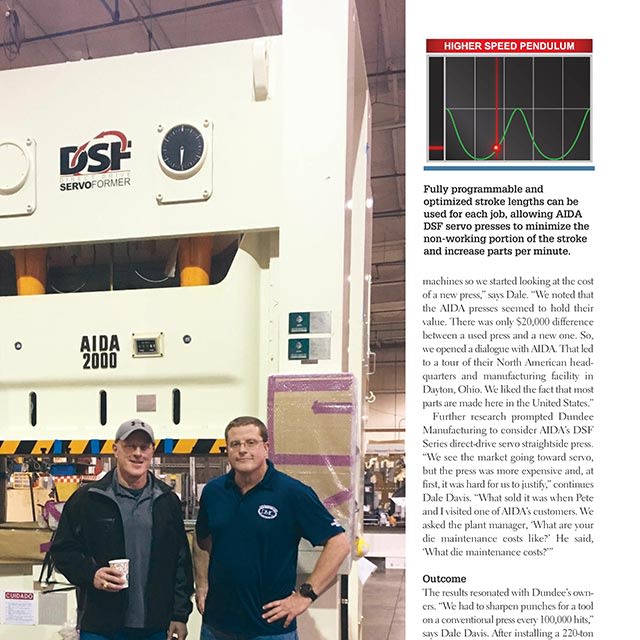
"We asked the plant manager, 'What are your die maintenance costs like?' He said, 'What die maintenance costs?'"
View User TestimonialEngel Diversified Industries
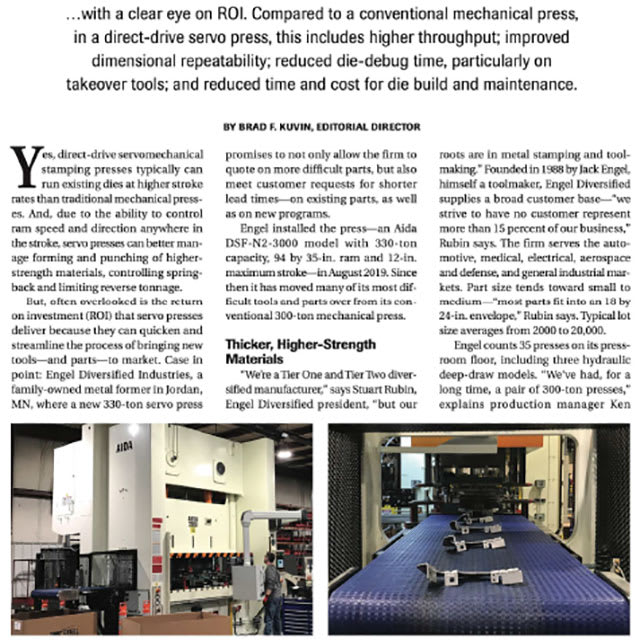
"We're running faster (pendulum mode), improving dimensional accuracy (stroke control, including dwell at bottom) and improving die life between sharpening (less reverse tonnage)"
View User TestimonialEngel Diversified Industries
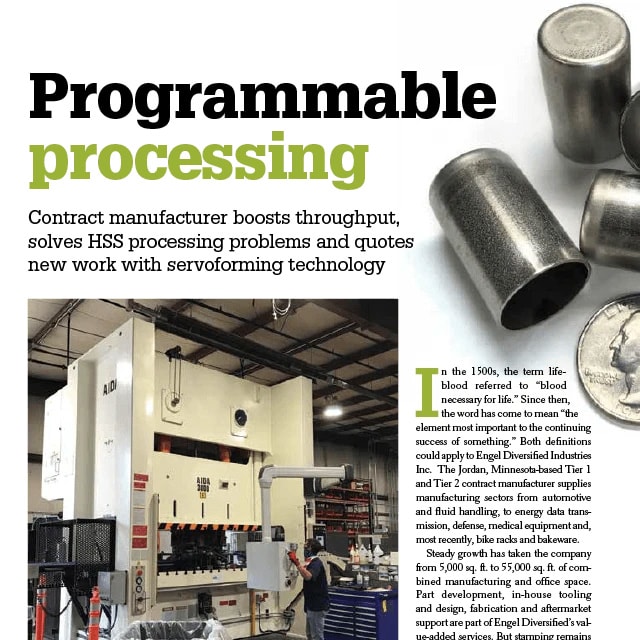
"We had some issues with wipe forming this part on a conventional press. When we processed it in pendulum mode, we found we could increase throughput by 60 percent."
View User TestimonialGrant Group
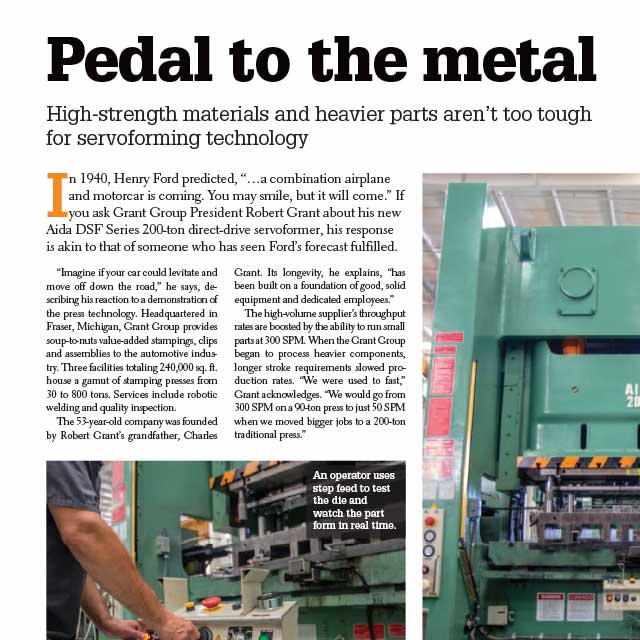
"The quality, speed and consistency of the AIDA direct-drive ServoFormer make it the press of the future."
Henderson Stamping
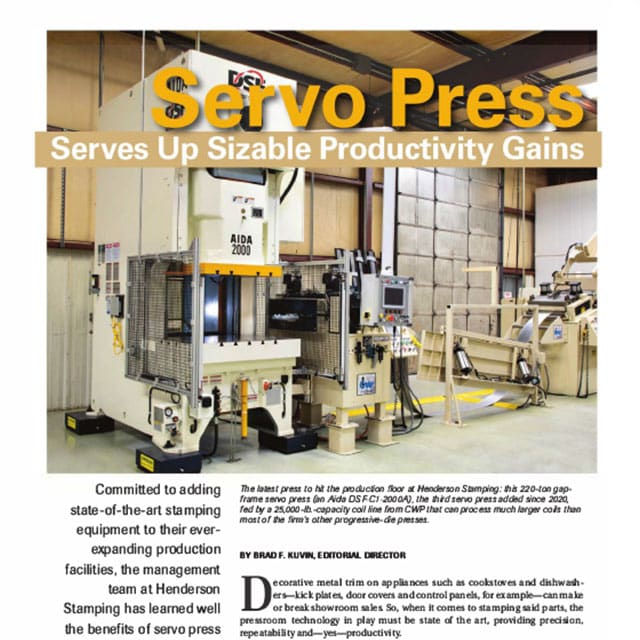
"AIDA was able to provide the perfect press for the job, including the control package we sought. It shipped and installed the press in just a matter of months. Their team knocked it out of the park."
View User TestimonialMeier Tool & Engineering
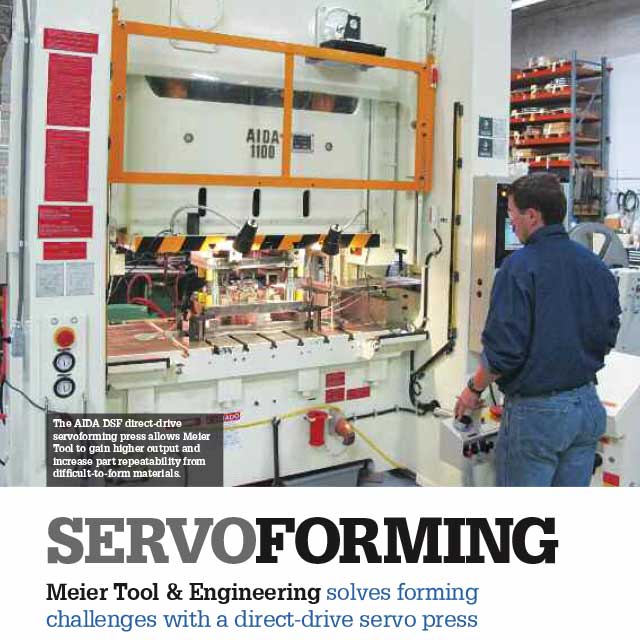
"We needed to be able to control slide velocity not only throughout the stroke but during bottom dead center work."
Metalstamp

"As a result of this flexibility we've begun to quote jobs we could not have considered in the past, such as pausing at a given point in the stroke to perform laser welding or component insertion."
View User TestimonialMidway Products
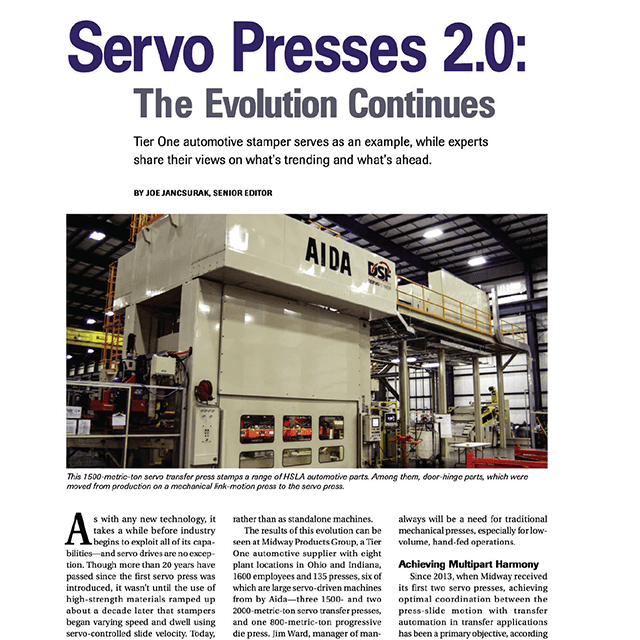
"With servo drives, the contact and draw velocity area infinitely variable, enabling dynamic motion profiles with multiple slow-down windows to allow the transfer system time to do its job. We're able to achieve this with the help of our equipment vendor, AIDA-America, who has, over the years, provided many rounds of training for our programmers and operators to ensure optimization."
View User TestimonialNewman Technologies
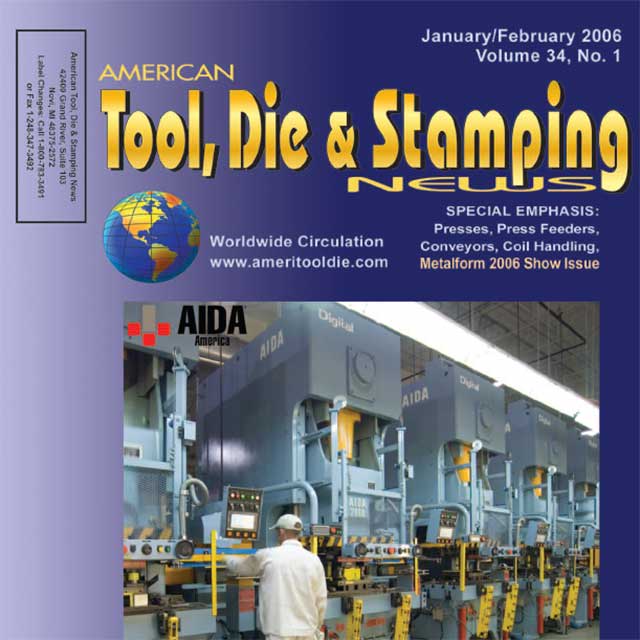
"We wanted a system that could not only produce the part but support our just-in-time initiatives by helping us to further reduce inventory, lead times and the cost and maintenance associated with progressive dies."
View User TestimonialOmex Manufacturing ULC
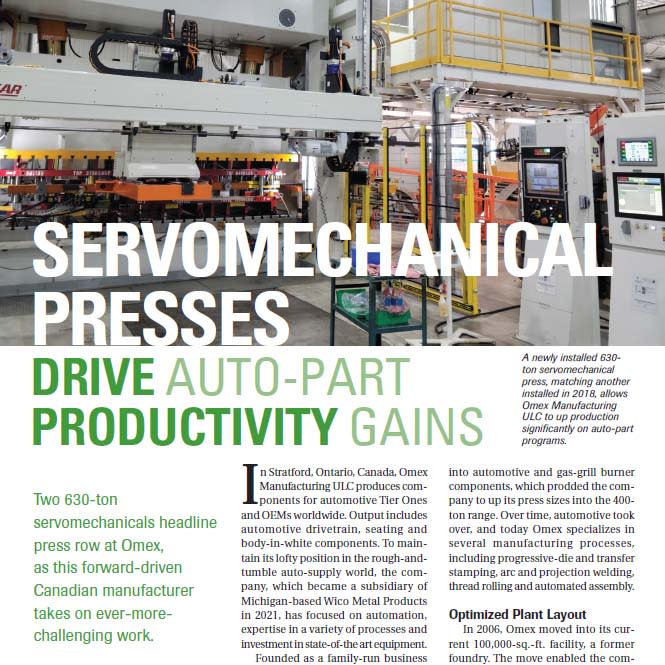
"We've just finished trialing an automotive-part program that previously ran at 25 strokes/min. We monitored the energy when forming at that rate, and by using pendulum motion to significantly cut back the dead (nonforming) cycle, we easily reached 40 strokes/min."
View User TestimonialPyper Tool & Engineering
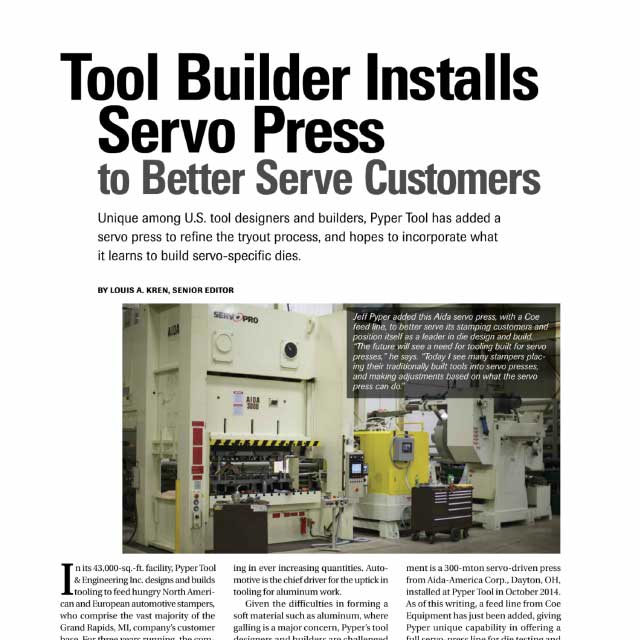
"I thought a long-term strategy would be to have a servo press in our die shop so that we could perform research and development and come up with some new techniques."
View User TestimonialQuality Metal Stamping
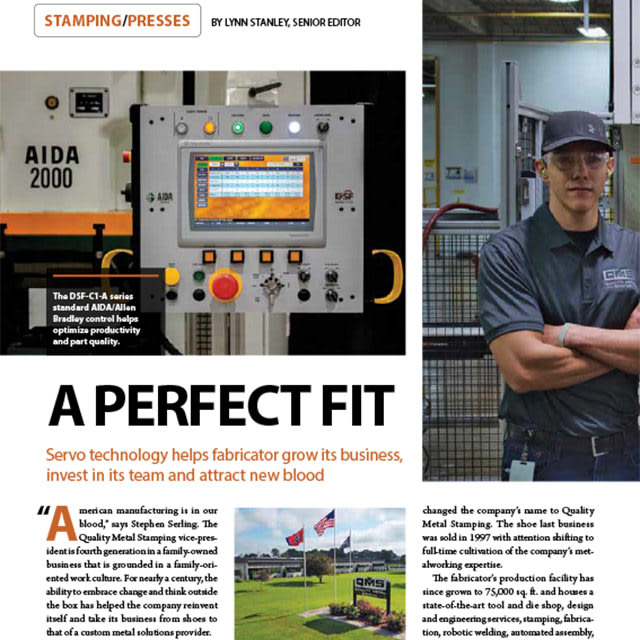
"We recognize that in order to stay competitive we need to invest in the latest metalforming technology. That meant considering a servo press versus a conventional mechanical press. We felt AIDA offered the best in the market."
View User TestimonialQuality Metal Stamping
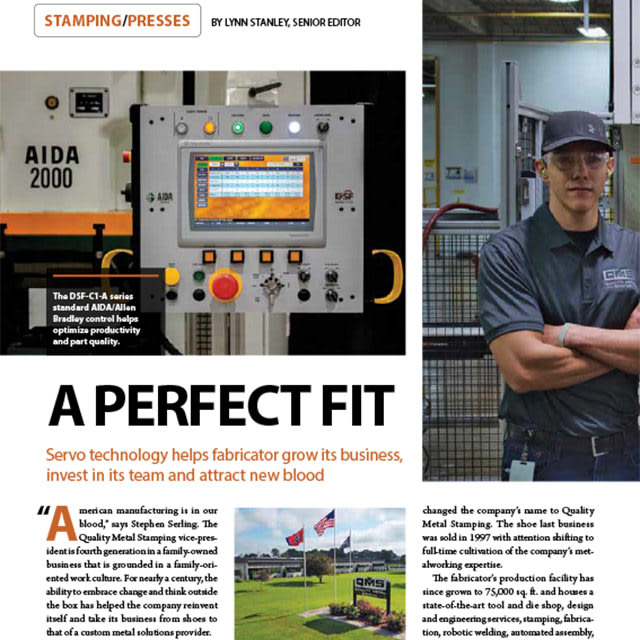
"We recognize that in order to stay competitive we need to invest in the latest metalforming technology. That meant considering a servo press versus a conventional mechanical press. We felt AIDA offered the best in the market."
View User TestimonialRoyal Die & Stamping
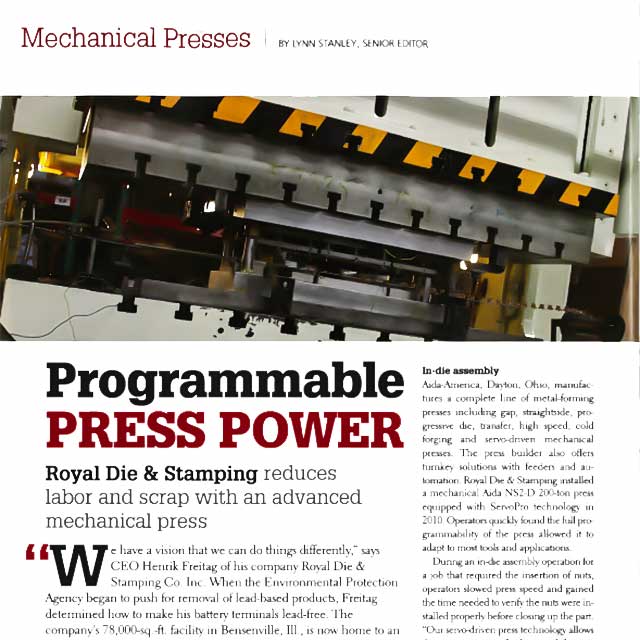
"The programmable stroke was a big help on this job, we could do the job on another press but we were having issues with the small punches breaking."
View User TestimonialScandic Spring
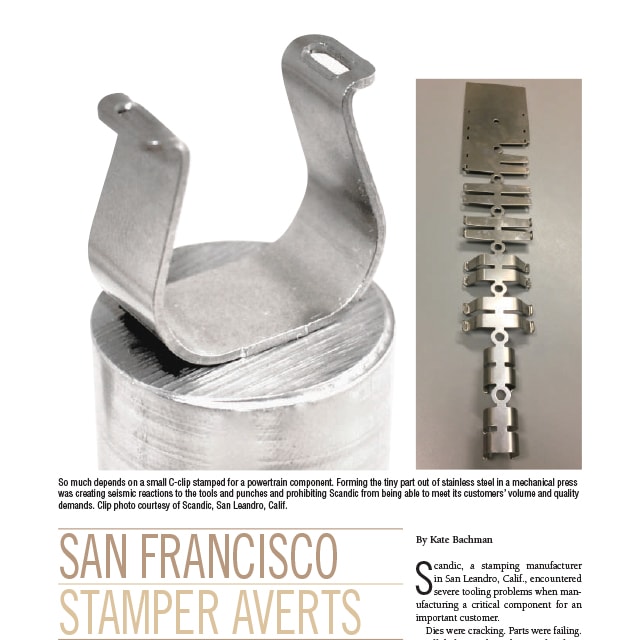
"This job really illustrates the benefit of slowing down the press at the bottom dead center [BDC] while still applying full tonnage."
View User TestimonialSmall Parts Inc.
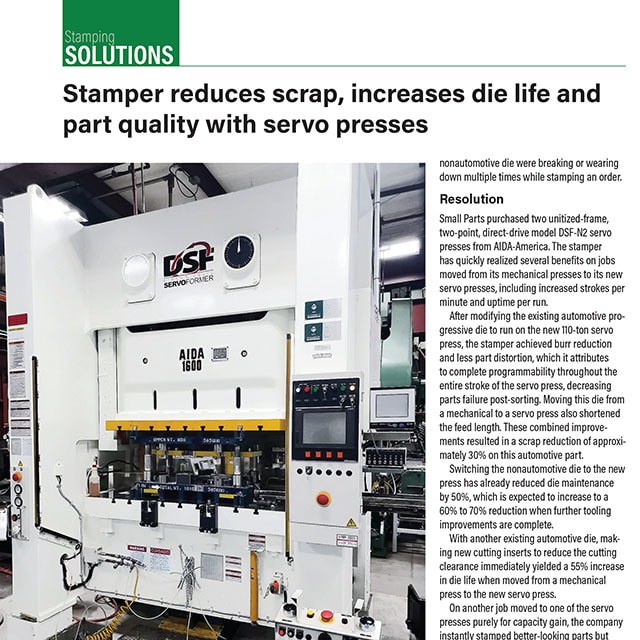
"Switching the nonautomotive die to the new press has already reduced die maintenance by 50%, which is expected to increase to a 60% to 70% reduction when further tooling improvements are complete."
View User TestimonialUltraform Industries
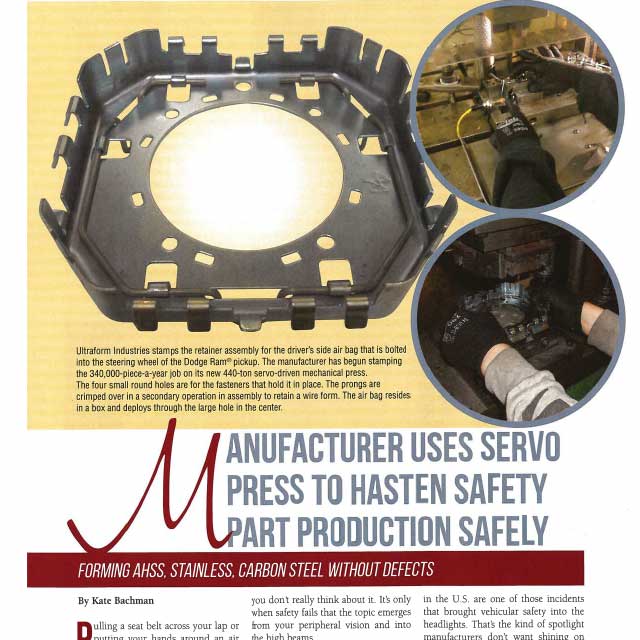
"Right now on the servo press, we're running about 54 strokes per minute. The best we could do on our mechanical press was 32."
View User TestimonialWard Manufacturing
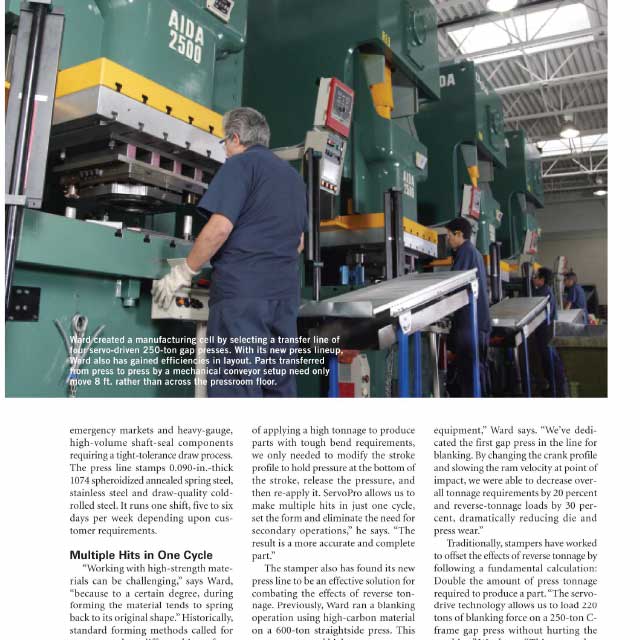
"It allows us to form more complicated geometries and produce draws in exotic materials at higher speeds while maintaining dimensional integrity - something that, prior to this technology - was, at best, difficult."
View User Testimonial